Rugged IP67 Rotary Encoders for Heavy-Duty Applications
Industrial applications usually involve challenging environmental conditions, which many sensitive measurement devices are not designed to handle.
Position feedback and displacement sensors such as rotary encoders are one example, as their electro-mechanical design with moving parts makes them particularly vulnerable.
Conditions that a Rugged Encoder Should Be Able to Withstand
If you are selecting an encoder for use in a heavy-duty application, or harsh environment there are 5 attributes that need to be considered:
- Ingress protection rating
- Resilience to shock
- Tolerance of vibration
- Ambient operating temperature
- Resistance to corrosive materials
Ingress Protection Rating
It is important that your encoder can withstand ingress from dust or moisture.
Many heavy-duty applications take place in environments, where one or both are present.
At a minimum your encoder should have either an IP66, or IP67 protection rating. IP68 or IP69 may be preferable if the environment is particularly damp or wet.
It should be noted that all four of the ratings levels mentioned above offer the same level of dust ingress protection, it is the level of moisture protection offered that varies.
Care should be taken to ensure that the encoder is installed in such a manner that water is deflected away from any vulnerable points in the installation, such as connector or cable joins.
If an encoder is installed with the shaft facing upwards, it is advisable to take step to prevent water from running down the shaft continuously.
Resilience to Shock
Encoders are often used on mobile machinery and heavy-duty equipment, such as mineral crushers. These machines are subject to a certain level of shock during operation. The encoder you select should be able to withstand the shock that is likely to travel through the machinery it is mounted on.
Vibration
Likewise, vibration is also likely to be an issue. Again, any encoder you select must be resistant to vibration in the application.
High temperatures
Some parts of the Australian continent can be extremely hot at certain times of the year, and some industrial environments, such us underground mines and metal processing facilities involve high ambient operating temperatures.
When selecting an encoder, it is important to check the operating temperature published in the data sheet is wide enough to encompass the ambient temperatures the device is supposed to operate in.
If you are selecting an encoder for mobile machinery that may be used in Australia you will need to check the lowest temperature, as well as the highest. Some parts of Australia can get very cold during the year.
An encoder should never be exposed directly to sunlight, or any other heat source. A hood, or ‘umbrella’ should be used to shield the encoder. Otherwise the temperature in the encoder could exceed the maximum rated operating temperature, which could cause damage to the internal components.
If an encoder gets extremely hot during the day and then extremely cold at night, there is the risk that contaminants such as dust, or moisture could be drawn into the encoder as the air inside contracts.
Resistance to corrosive materials
Some industrial and process applications involve the use of corrosive materials. If there is the likelihood that the encoder could come into contact with these materials, you will need to check what material the encoder housing is constructed from, to ensure it will not react with the corrosive material in question.
If an encoder is to be used in an underground mining application, it is important to check there are no restrictions as to what materials that the encoder may be constructed from.
The use of aluminium may be restricted as there is the possibility that high energy impacts of aluminium alloys on rusty steel objects can cause a spark, which could ignite explosive gases.
Mine water can be corrosive. In addition to mine water and coal corrosivity, the presence of bacteria leading to microbiologically influenced corrosion can also be a factor. Common bacteria that cause corrosion in mines are sulphate-reducing bacteria and acid-producing bacteria. These can even cause stainless steel to corrode.
Encoders offered by PCA, are constructed from several types of material, so in most cases, we should be able to offer an encoder that is suitable for mining applications
Heavy Duty, Mill Duty and Severe Duty Encoders for mission-critical rugged applications in Australia
Avtron Encoders
“Anywhere an encoder failure would cost money and downtime, you need an Avtron Encoder” – Avtron Encoders
The Avtron encoders are heavy-duty encoders specifically designed for rough and rugged operations. Avtron offers products with both magnetic and optical encoders, all physically large offering a level of robustness for the most rigorous of environments.
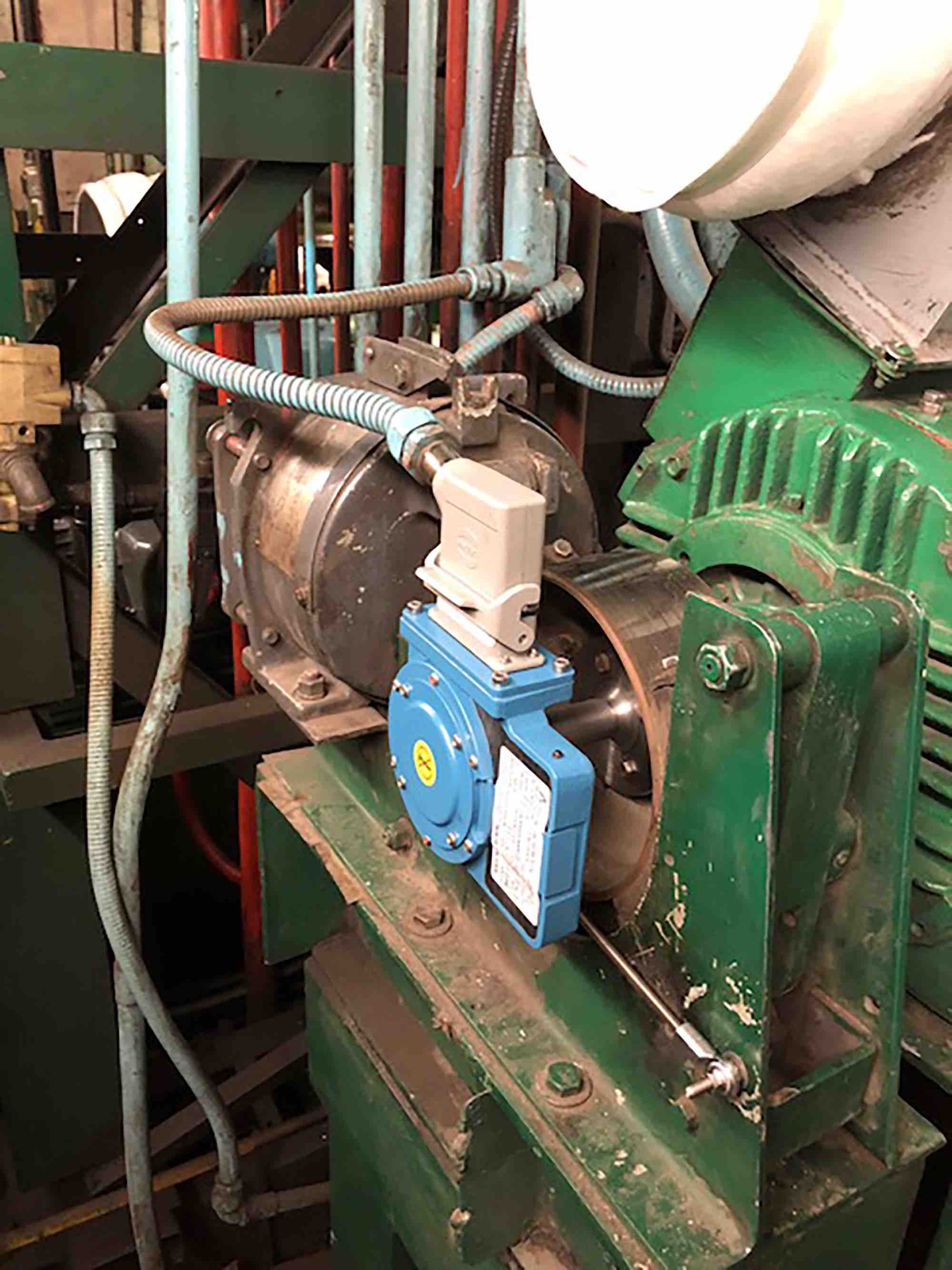
Avtron Encoders feature die-cast aluminium housing, potted electronics and huge bearings (even some featuring no bearings). Many of the Avtron Encoders also feature onboard diagnostics, offering users self-tuning for the best signal and alarms to notify users of problems.
The Avtron Encoders are incredibly durable for a range of environments, some featuring operations temperature ranges from -40 to +85 degrees Celsius.
The Avtron Encoder line provides users with options within both magnetics and optical encoders, with both incremental and absolute within the distinct lines.
If you have a rugged application requiring heavy-duty encoders, the Avtron Encoders may be the right solution for you.
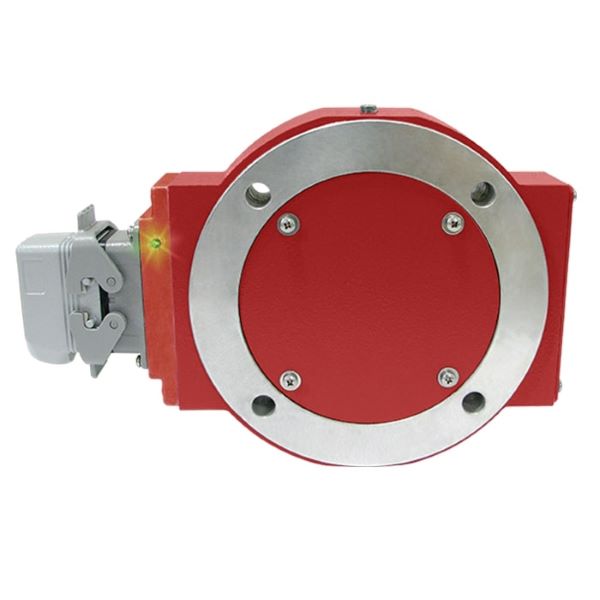
PCA Encoders
PCA Encoders (an ADM Systems Group company) are Australia’s encoder specialists and we stock rugged encoders for use in harsh environments.
For example, the IPHJ series encoders from PCA is one of the most popular through-hollow shaft encoders, because of its proven reliability and ease of mounting.
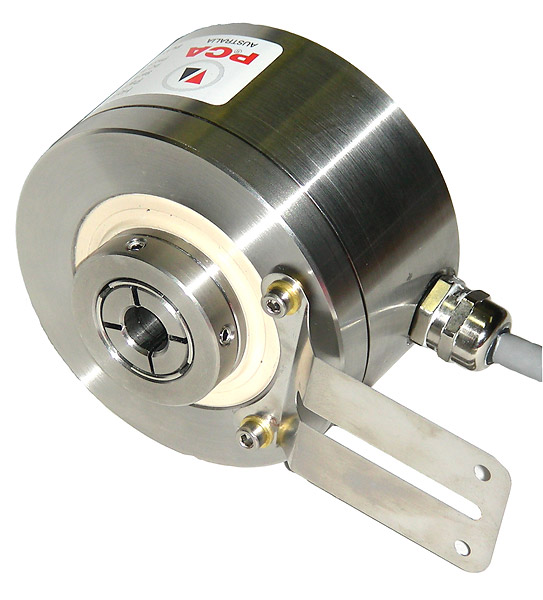
The IPHJ series encoders are commonly found mounted directly onto the shaft of industrial AC induction motors. An all stainless-steel body and sealed stainless shaft design, ensures a high resistance to corrosion. It also has an IP67 ingress protection rating, so it is resistant to dust and moisture ingress.
One example of such an application is outdoor overland conveyors. These are subject to high levels of dust, vibration and operate in high temperatures. These conveyors require speed following, running the motors with a variable speed drive (VSD) in closed loop control. Reliability is important in these applications as a failure can affect an entire operation.
Another application these encoders are used in is speed feedback on industrial washing machines, where vibration and corrosive chemicals are commonplace.
PCA also represents POSITAL in Australia.
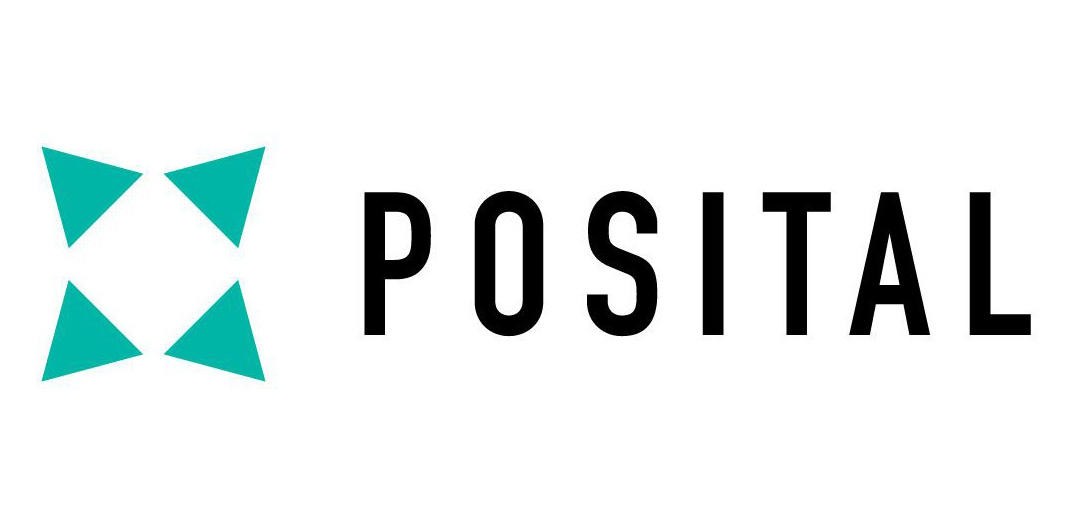
POSITAL offers an incredibly wide variety of encoder options to choose from, so your application requirements are likely to be met. The handy POSITAL Product Finder is featured on the PCA website.
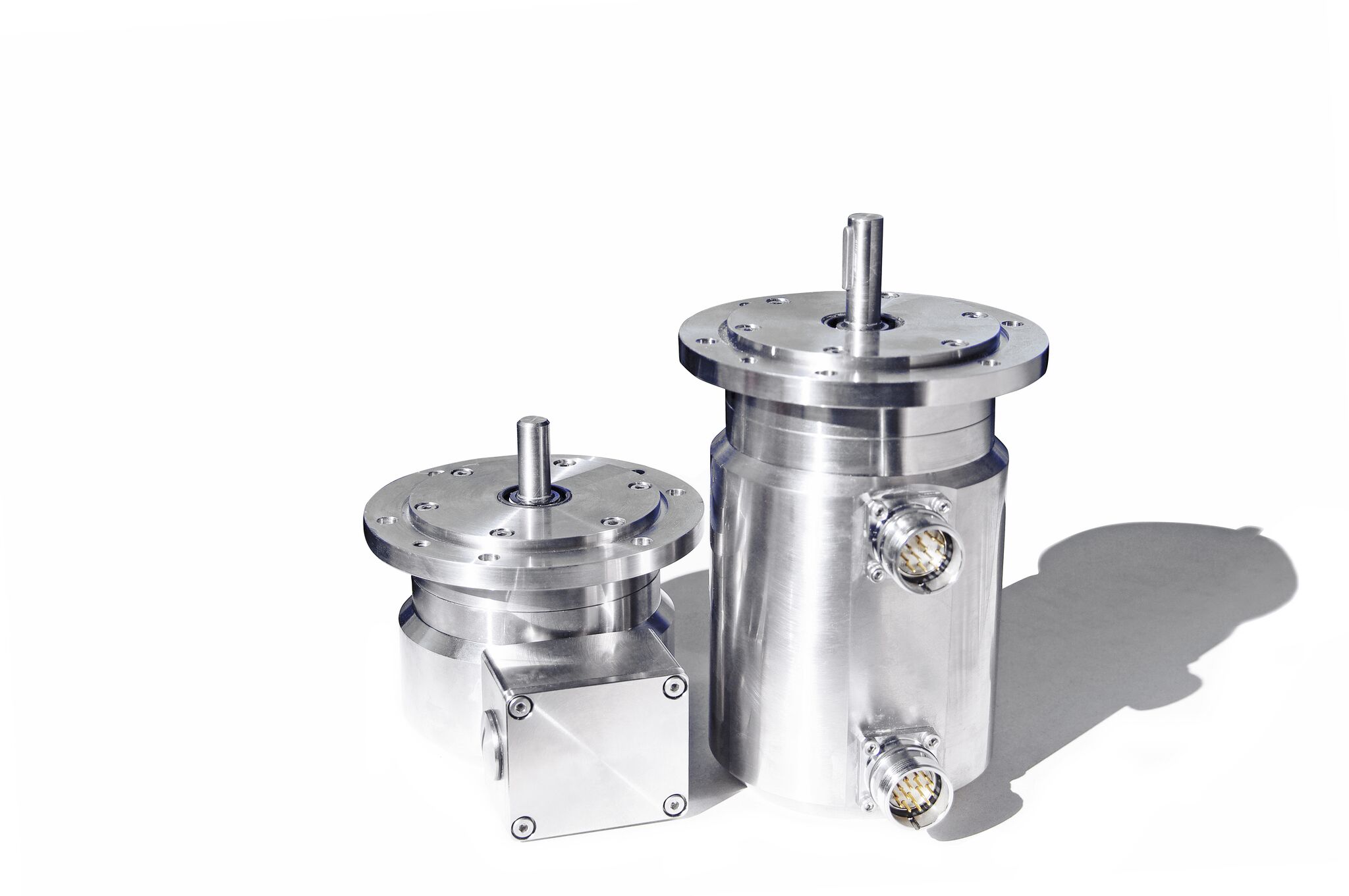
POSITAL’s heavy-duty extra rugged 316L stainless-steel IP67encoders meet very high standards and incorporate features like:
- High mechanical shaft loads (up to 250 N Axial, 350 N Radial)
- High shock and vibration impact (200G and 20G Respectively)
- Shaft-lock mechanism to protects internal components
- Dual-function mode with incremental and absolute outputs
Selecting an Encoder for Use in a Harsh Environment
If you would like assistance in selecting an encoder that is suitable for use in a heavy-duty application, then please do not hesitate to contact PCA Encoders.
IS THIS INFORMATION USEFUL?
If so, why not share it with your peers and colleagues. Simply click on the blue LinkedIn share icon below.